Advanced designs and detail fittings
The
designs in this section represent several years of
working with PVC and copper fittings and also
many ideas from builders I have corresponded with.
I have selected my favorite versions and removed some
of the older
postings.
One of the first negative comments that I received
regarding the 20-20 design in 2001 was the perception that it was
" Flimsy". I don't think it was so in that it was not intended to
to be a strong or long lasting model. It was ,and is ,intended
to help sailors experience the joys of self-steering with
minimal expenditure of time or material. However, I found that
many who were interested in building one wanted to build a
model for real sea going use. I think these designs will do that.
The perception that copper is "Soft and weak "is going to
take some explaining. I have done tests and stress analysis to
convince myself of the benefits of these designs. See below.
Think of these designs as a simple way to get a rugged model
without having to build in stainless steel.
I have not yet included CAD drawings of these ideas
on the assumption that anyone wanting to tackle
these designs will have the level of skill to build from
just the scanned sketches and related photos.
If
you would like the CAD files
that these JEPG files were scanned
from please contact me.
These designs have been built as prototypes and
were used to evaluate the construction methods
using PVC and copper plumbing parts. They have
had limited sailing time but seem to work well.
Two of these designs are based on ideas presented by
Jan Alkema in several boating publications but in my opinion
have not had the publicity they deserve. The USD ( up side
down ) vane is a concept that improves performance and
the RHM ( rudder head mount ) is a fine solution to mounting
a pendulum type device on outboard or transom rudders.
It is a challenge to understand but once you see the elegant
simplicity of the scheme I think you will agree.
Model 2004
November 2003
I consider this a logical evolution of the 20-20 idea of a cheap,
easy to build self-steering design that will allow the sailor with
normal hands on skills to build a device that that will have
very good performance and be capable of rough water use.
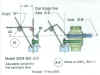
Model 2004-A Model
2004_1.0 Model 2004_2.0
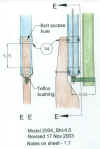
Model 2004_2.1 Model
2004_3.0 Model 2004_4.0
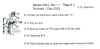
Model 2004 notes
This version obviously reflects my experimentation with PVC
and copper parts. It also provides some features that have
been needed such as --
A way to quickly stow the oar out of the water
when using a motor to move the boat in reverse around docks
or mooring piling . The entire oar and it's carrier will rotate to
a vertical position without removing or disengaging any lines
or fittings. Just rotate the oar to starboard until it points up
and tie it off in the inverted position. A photo of similar design
shows how it worked on my boat.
The model 2004 oar carrier is based on simple PVC fittings
and simple input linkage from the wind vane. The support frame
is copper pipe and soldered fittings for a rugged mounting base
that is easy to build and very inexpensive. No special tools or
construction skills are needed.
Photos to be added here showing prototype construction
details
Combining these water side
parts with a USD wind vane should produce a system to steer
most boats better than many commercial products and do it
for a fraction of the cost.
Model 90-95
Bevel gears to allow rotation of carrier
to a safe stowage position. Shown here with a copper oar carrier
and hinged oar.
The 90-95 design with
copper tee fittings will require the removal of the stop material in
three fittings to allow the shaft to pass through. This is easy for a lathe
but can be done by hand with a round file or rotary bit and a hand
drill.
Model 90-93 Jan Alkema invention----
RHM
The sketch below shows the basic idea and the numbers
are typical values. Several linkage arrangements have been
used. The original model uses small wire rope from the vane.
Check the last of this page for a write up he did for
Practical Boat Owner The publisher has no objection to
the
use of the material here.
I refer to this as a RHM for rudder head mount.
This idea is for transom
mounted rudders and has no lines in
the cockpit or to the tiller.
This concept of Jan's is hard to
visualize at first look
but it is a really unique scheme that he
has used with much
success for many years. The line to the
blue carrier I call
a " Floating link ". It acts to provide a pivot
point about which the oar
load is reacted. This causes the
upper hinge of the oar to
load the carrier hinge causing a
torque on the rudder. To
disconnect the gear ,the lines are
released at the
cleats and the oar will then trail along.
A rigid link
with self aligning ends will do the same function
and might be
used to clear an outboard motor or swim
platform.
I suggest
that a simple model will reveal the action of
the oar on
the rudder. The oar is not a trim tab as it
might appear.
Since the oar is rotating with the rudder
a negative
feed back is required to compensate for
the angle of
incidence and if needed provide more
negative
rotation to provide stability.
Fin keels and
rudders without a skeg on many boats is a
challenge for
many self-steering devices but his one has
proven that
it capable .
A side mounted vertical vane
connected to a rudder head that required only minor work for
the support shaft of a simple carrier design. The builder converted
to this arrangement from a trim tab system.
This is a simple linkage and oar carrier that will allow
the push rod input from the wind vane to be from any
direction. This means that the vane can be mounted
off to one side or above if mounting space is a problem.
The small displacement of the crank input point due to the
rudder turning will have minor effect on the oar.
Model 90-93_Linkage-3
This is the linkage shown mounted to the
red mock up rudder head. It is driven by the input arm
at the rear and turns the oar through the sliding plastic
( Teflon or Nylon ) blocks. The supporting trestle
is made of one half inch copper pipe and screw fastened
to the rudder head. The push rod input from the vane is
located near the rudder hinge line to minimize any unwanted
input to the oar tiller.
Model 90-93_Linkage-5
This shows the oar carrier pivoting on a stainless
steel tube supported by a fitting fastened to the
rudder head.
Model 90-93_Pic-9 with another oar tiller/crankshaft
fitting and painted with aluminum spray paint to look like stainless.
Model 90-93_Sht-110
The supporting frame for the USD vane uses the same
material and techniques as the other copper frames
and is attached to the boat's stern rail.
Model 90-94 USD vane system--- Another Jan Alkema
Model 90-94 _Sht 1a
This USD design is recommended for
all models.
The details are from other pages
and the
course setting is shown in detail on the
20-20 pages
with photos and drawings.
This version
uses a larger base to adapt to the
copper
frames. The push rod and vane linkage
has
proven to work very smoothly.
Model 90-94_Sht 1b
The tilted vane shaft carrier is made from 1-1/2 inch
(USA ) PVC pipe. A 1-7/8 hole saw makes a perfect
fit through the 2 inch mast. Very minor trimming may
be required if the holes are not exactly aligned.
Press fit the two and use Pvc caps for the shaft
bearings. Ball bearings could be used here but the
PVC will be quite satisfactory.
The simple shaft through the mast post is returning
to the 20-20 level ( Bird House Technology ) that has produced
many very satisfactory gears for builders world wide.
This is taking the RHM and USD ideas to combine in
a unit with all mounted to the boat's rudder. The turntable mount
is restrained in rotation by an arm as shown in the diagram layout.
the rudder turns per the normal RHM but the USD assembly is
not allowed to follow or rather maintains it's set direction except for
the minor and insignificant amount shown.
The weight of the USD parts and their supports can be built to
be less than 15 Pounds. It can also be built to be quickly removed
from the rudder as a unit.
The direct push rod from the vane crank to the crankshaft arm
will avoid slack wires or difficult adjustments and of course allow a full
360 degree course setting rotation. Vane
support made from PVC cap fittings
mounted on aluminum post. Opened for photo showing over
sized hole in tube to clear crank rod which turns in the PVC caps.
Close up of retaining screw in mast post
Jan's explanation of the rudder mounted design.
An
innovative pendulum system for outboard rudders.
Jan Alkema
03-05-2005
Preface
On boats with outboard rudders
it can be troublesome to install a pendulum windvane system. The pendulum
has to be free of the rudder and should not limit the rudder movements from full
port to full starboard. That means that an extended support frame will be
necessary. It will put extra weight on the transom. Another obvious drawback is
that the wind vane system has to be mounted further aft of the boat, which makes
it more vulnerable in harbors and crowded marina’s.
A lot of sailing boats with an outboard rudder and
wind vane system make use of a trim tab, directly mounted at the rudder. The
trim tab works as a servo system to generate enough force to turn the rudder.
It is unquestionable that a trim tab with the right
dimensions works, but on some points its performance is less than that of the
pendulum system.
Trim tab or pendulum.
Let’s compare the characteristics of a trim tab and
a pendulum system and focus on the following aspects :
·
Steering torque
·
Steering efficiency
·
Yaw damping
·
Support and vulnerability
·
Obstructions in the cockpit
Steering torque.
The trim tab can be situated just at the trailing edge
of the rudder or at some distance of it. This
choice is mostly depending on the shape of the rudder. In figure 1. the trim tab
is directly mounted after the trailing edge. In figure 2. the trim tab is
mounted some distance behind the rudder.
In both cases the trim tab is working in the wake of
the rudder. The solution of figure 2. has the advantage of giving a bigger
torque, due to the increased distance between trim tab and rudder hinge.
The pendulum has normally a larger power arm as can be
seen in figure 3. So the pendulum with the same dimensions of the underwater
part as the trim tab, delivers more torque. This can be advantageous for heavy
or unbalanced rudders. Pendulums can operate these rudders without problems, but
trim tabs can be limited in their steering torque.
Steering efficiency.
A trim tab develops a force which direction is
opposite to the rudder force. The trim tab is decreasing to some extend the
effect of the rudder. With normal dimensions the loss of rudder force is approx.
10 %. So the trim tab makes the
rudder less effective.
The pendulum force works in the same direction as the
rudder, so it assists the rudder and increases the total rudder action and hence
the steering efficiency.
Yaw damping.
Yaw damping is the ability to prevent or reduce oscillations
in the course. Lack of this ability gives a zig - zag course, so it is an
important characteristic of a course controller.
Yaw damping is not easy to explain, but the following
example may help to get an idea of it. In this example we are only considering
the influence on the rudder and we suppose that the vane is not turning during
the yawing motion of the boat.
When wave and/or sail forces are turning the boat (
yawing) , then there will be pressure on the rudder from the water flow.
When the rudder is fixed a force is developed on the
rudder which counteracts the yawing motion.
When the rudder is free, then it will line up with the
water flow and does not give any counter force to the yawing motion.
A rudder with a trim tab is not fixed or free but
controlled by the trim tab. When the boat yaws the water flow creates a force on
the rudder + trim tab and initially the rudder tends to line up with the water
flow and rotates a bit. But the trim
tab gets a greater rotation (in the
same direction) due to the linkage between trim tab and wind vane. The water
flow on the deflected trim tab creates a force
which prevents the rudder from lining up with the water flow. As a result of it
the rudder gives some counter force, which
damps the yawing motion.
This counter force is however smaller than a rudder
alone, that had been fixed.
A pendulum system, connected to the rudder can give
more yaw damping , and most when the pendulum is far aft of the rudder out of
the wake. When the boat yaws the rudder and the pendulum get a pressure from the
incoming water flow. The pendulum wants to swing out and the rudder wants to
line up with the water flow. But because the pendulum is much more powerful then
the rudder it swings out and turns the rudder opposite to the water flow
direction. So instead of limiting the rudder angle from giving in (this is what
the trim tab is doing), it increases
the rudder angle to create an increased counter force. So the pendulum system
gives a powerful and active yaw damping. The counter force of a rudder +
pendulum is bigger than a rudder alone that had been fixed.
This is true when the pendulum is out
the wake of the rudder. When the pendulum is close to the rudder then the active
yaw damping effect is less. But it
is always more than from the trim tab, because when the pendulum swings out, it
brings the blade far more out of the wake of the rudder compared with the trim
tab.
Support and vulnerability
An advantage of a trim tab system is that no heavy
support is necessary. The trim tab is directly mounted at the rudder.
The trim tab is well sheltered by the rudder which is
an advantage compared with a pendulum, which swings out and can pick up weed,
ropes and floating debris
As already mentioned an extended support frame is
inevitable for the normal pendulum system for an outboard rudder.
Obstructions in the cockpit.
The trim tab system has no steering lines and blocks
to the tiller or wheel. The trim tab directly controls the rudder blade.
For normal pendulum systems steering lines with
several guiding blocks are running through the cockpit to operate the helm or
the steering wheel. This is mostly a nuisance in the cockpit.
Combining the advantages.
My boat, a Westerly Konsort, has an outboard rudder.
When I started to design a wind vane system I wanted to have the best of both
worlds. So the advantages of a pendulum system should preferably be combined
with the advantages of a trim tab system. Would that be possible?
After many sketches and a lot of thinking I came up
with a system which I later named the Rudder Head Mounted (RHM) pendulum
or oar system. See the sketch in figure 4.
The pendulum has the horizontal hinge mounted on the
rudder head.
Essential are the two restraint lines from the transom
side to the oar carrier or pendulum tube. When these lines are loose, the
pendulum can swing to each side, but it can not turn the rudder. The system is
disconnected. When these restraint lines are tight, then they form a fixed point
on the tube which will be a pivot point. (point
P) When the pendulum swings out then the rudder is forced to turn.
Figure 5 shows how the swing out movement of the
pendulum gives a rudder movement, when the restraint lines are tight.
For stretching or adjusting the restraint lines I use
clam cleats on the aft cockpit sole. To release the lines, simply pull them out
of the cleats.
This Rudder Head Mounted (RHM) pendulum combines all
the advantages of both the pendulum and trim tab :
·
It is a true pendulum with the
power of normal pendulums.
·
It increases the rudder action.
·
Yaw damping is better than with a trim tab
·
No heavy support frame is
necessary.
·
There are no steering lines in the cockpit
One minus point remains. The pendulum
is not so well sheltered after the rudder as the trim tab.
I made the prototype of the oar carrier and the oar from
plywood. I used SS hinges which are normally used for the rudders of small
dinghy’s. The first sailing tests were carried out
in 1981 and it worked from the start.
Figure 6 shows the prototype
of the oar carrier and oar, which fitted very well with the shape of the rudder.
This RHM pendulum system is combined
with a separate wind vane which is mounted on the push pit. Via thin stainless
steel cables the rotation of the vane is transmitted to the little tiller on the
oar.
Figure 4 shows how the cables are
running from the wind vane to the small tiller arm on the oar.
I used the prototype of the RHM pendulum for some 5 years.
After that I have rebuilt the system, using stainless steel tubes. Ball bearings
are used for the oar rotation and in all blocks to get as low friction as
possible. I also made the blade retractable. It is still in use, after 20 years,
with only small modifications up to now. See figure 7 and 8.
Position of the cleats for the restraint lines.
The position of the cleats should be close to the
sides, using the full width of the transom. The restraint lines have to remain
reasonable tight without slack or over tension for rudder angles of
+/- 20 degrees, which is the max. range for rudder corrections during
sailing.
On my boat it appeared that the cleats should be
positioned higher than the connection point
P on the oar carrier or
pendulum tube. On my system the vertical distance between P and the cleats is
about 0.25 m.
In general it may need some trial and
error to find the best positions of the cleats.
Well mannered behavior.
On every pendulum system the oar needs
feedback, otherwise the system will over steer.
When the oar is initially turned by the vane, it will swing out, but
during that swing the oar is rotated back, to arrive at a certain swing angle
and so at a certain rudder angle. The information of the swing angle is fed back
in the turning of the oar through the linkage between vane and oar.
The RHM pendulum system needs more feedback than a
normal pendulum, because the pendulum rotates together with the rudder, so that
rotation must also be compensated as an extra.
The geometry of the cross beam and wires and blocks
however ensures that there is more then enough feedback in the system, to get a
well mannered behavior of the pendulum without any sign of over steering.
The system gives a good yaw damping in downwind and
broad reaching courses on a lively boat like the Westerly Konsort. Note the
straight track on figure 9 during a running course in force 5.
On windward courses the system works also very well.
Note the oar at work, most of the time out of the wake
of the rudder in figure 10.
The wind vane part.
Up until now the wind vane part has not been highlighted.
The wind vane part has been developed separately from the pendulum.
Before starting with the RHM pendulum I used a big wind
vane, directly coupled to the rudder. I had taken that wind vane from my
previous boat. It had an adjustable vane axis tilt angle. An article on that separate
wind vane has been published in PBO nr. 170
Febr. 1981.
After building the RHM pendulum I
combined it with the existing wind vane. The combination worked very well,
although the vane was a bit oversized for operating the small oar.
Some 6 years ago I designed a new type of wind vane,
the Up Side Down (USD) wind vane,
which could easily be connected to the existing RHM pendulum via the thin
stainless steel wires.
See figure 11.
The interesting feature of the USD
vane is that the vane action
increases when the boat heels. It automatically adapts its action in the right
way to the sailing circumstances.
When heeled with some weather helm, the USD vane gives more
action for a better accuracy. On a downwind course with no heel the USD vane
action is less, which enhances course stability.
The USD wind vane has been described in the article “
Which wind vanes work best “ (PBO nr. 414 , June 2001) .
How to operate the RHM / USD system.
At the start the vane is locked is a vertical position
and the restraint lines are slack, the blade is put into the water. It appears
that the oar is following the rudder without swinging out, also when the boat is
steered manually. With slack restraint lines no forces are exerted on the
rudder.
When the restraint lines are tightened
and the vane is set on the desired wind course and released, then the
system is taking over and will steer the boat.
Normally I put the tiller in the upright position to get a free and
uncluttered cockpit.
To disconnect the system I first lock the vane in a
vertical position and then pull the restraint lines out of the cleats.
Conclusion.
The described construction principle
of the Rudder Head Mounted pendulum has been used for 25 years now. I made many
sailing trips with it to Denmark , UK and France.
Up till now I have not experienced any shortcomings in the system.
In my opinion it is a feasible and
satisfying solution for boats with outboard rudders.
RHM and USD are working together
perfectly, making sailing trips even more enjoyable.
Posted on this site on 5 June 2005 with minor spelling
changes
|